Foam Moulding: An Overview of Polyurethane Foam Applications
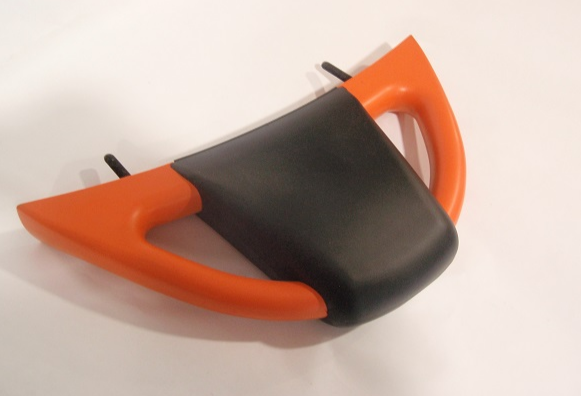
Foam moulding, particularly polyurethane foam, is an advanced technology used for producing versatile and durable products in a wide range of industries. At the heart of this innovation lies polyurethane foam moulding, which includes methods such as Integral Skin Moulding and Self-Skin Moulding. Polyurethane foam products are known for their softness, durability, and flexible properties, making them ideal for various applications. This article will explore the intricacies of foam moulding, focusing on the benefits and applications of polyurethane foam in modern industries, and the significant role it plays in shaping everyday products.
Understanding Foam Moulding and Polyurethane Foam
Foam moulding refers to the process of using foam materials, particularly polyurethane foam, to create products with specific designs and properties. Polyurethane foam, in particular, has gained prominence due to its unique combination of lightweight flexibility and strength. It is extensively used in Integral Skin Moulding, where a dense outer layer, or “skin”, is formed during the moulding process, encapsulating a softer, micro-cellular core. The result is a foam that offers both flexibility and durability, making it suitable for a wide range of applications.
At Acoustafoam, with over 36 years of experience, they have perfected polyurethane foam moulding, producing products that meet high standards of quality. The company specializes in creating Integral Skin PU foam, which is commonly used in various industries for products like grab handles, armrests, and other furniture components. The strength and flexibility of the outer skin of the foam ensure its resistance to wear, tear, and abrasions, making it ideal for demanding environments.
Benefits of Polyurethane Foam Moulding
Polyurethane foam moulding offers numerous advantages, making it a top choice for various industries. Below are some of the key benefits:
1. Durability and Longevity
The primary benefit of polyurethane foam is its remarkable durability. The outer skin formed during the moulding process is tear-resistant, providing excellent protection against scratches, wear, and abrasions. This makes foam moulding an ideal choice for applications where long-lasting, robust performance is needed, such as in automotive components, furniture, and safety products.
2. Versatility in Design
Polyurethane foam can be molded into various shapes, sizes, and textures. The flexibility of the foam allows for intricate designs, from soft cushions to rigid structural components. Companies like Acoustafoam can even customize the texture of the foam’s surface, offering leather-like finishes or patterned textures for aesthetic appeal, which is particularly useful in the automotive and furniture industries.
3. Sound Insulation and Acoustic Benefits
One of the standout features of polyurethane foam is its acoustic properties. The foam absorbs sound waves, reducing noise levels and enhancing acoustic performance. This makes it a popular choice in industries such as automotive, marine, and construction. Additionally, foam moulding is also used in creating acoustic barrier products that help reduce airborne and impact sounds, improving noise control in various applications.
4. Customizability for Specific Applications
With foam conversion processes like cutting, slitting, CNC profiling, and die-cutting, polyurethane foam can be precisely tailored to fit specific needs. Whether it’s custom packaging, cushioned seating, or insulation, polyurethane foam can be converted into almost any shape or form to suit unique requirements.
5. Lightweight and Energy Efficient
Polyurethane foam is not only lightweight but also highly energy-efficient due to its insulating properties. This makes it an ideal choice for thermal insulation in various applications, including buildings, vehicles, and appliances. The foam’s ability to retain heat or cold helps reduce energy consumption, making it an environmentally friendly choice for many industries.
Applications of Polyurethane Foam Moulding
The versatility of polyurethane foam means it can be used in a wide range of industries. Here are some of the key sectors benefiting from foam moulding technologies:
1. Automotive Industry
In the automotive sector, polyurethane foam moulding is used to create components such as grab handles, armrests, headrests, and gear knobs. These parts benefit from the foam’s ability to provide both comfort and durability. The Integral Skin PU foam used in automotive applications is particularly advantageous due to its robust outer skin, which resists abrasion and offers a comfortable, soft touch on the interior components.
2. Furniture Industry
The furniture industry also relies heavily on polyurethane foam for the production of seating components such as cushions, armrests, and backs. The foam’s ability to maintain its shape while offering comfort makes it an essential material for sofas, chairs, and other seating products. Additionally, foam moulding allows for the production of decorative trims and finishes that enhance the visual appeal of furniture.
3. Marine and Aviation
Polyurethane foam is used in the marine and aviation sectors for insulation, seating, and safety products. The foam’s resistance to wear, moisture, and UV radiation makes it particularly suitable for harsh environments such as engine rooms or outdoor seating on boats and aircraft. Acoustic foam and impact foam are used extensively to dampen noise and improve the comfort of passengers.
4. Safety and Industrial Applications
In industrial settings, polyurethane foam moulding is used for safety products such as helmets, pads, and protective gear. The foam’s shock-absorbing properties make it an ideal material for products designed to minimize injury. The self-skinning nature of the foam helps create durable and protective products that withstand heavy use in construction, automotive, and other industrial fields.
5. Acoustic and Soundproofing
Polyurethane foam is frequently used in acoustic foam soundproofing products, which are crucial for controlling noise in a variety of environments. These include recording studios, home theaters, and public spaces where sound clarity is essential. The foam’s ability to absorb sound waves, especially at mid- to high-frequencies, makes it highly effective in reducing unwanted noise and enhancing acoustics.
The Foam Moulding Production Process
The production of polyurethane foam moulding involves several key steps:
1. Mixing and Chemical Reaction
The process begins with mixing two parts of polyurethane chemicals. Once combined, a chemical reaction occurs, causing the foam to expand and take shape within the mould. This reaction forms a product that has the desired properties, including hardness, density, and tear strength.
2. Moulding and Curing
After the foam is dispensed into the mould, it is left to cure, allowing it to solidify and take the final shape. The Integral Skin PU foam forms a tough outer skin during this process, which provides added durability and protection. Once cured, the product is removed from the mould, and any excess material (known as flash) is trimmed off.
3. Final Inspection and Quality Control
Once the product is fully cured and trimmed, it undergoes a series of quality control tests to ensure it meets the required standards. This includes checks for density, hardness, tear strength, and other properties. Only once these tests are passed is the product ready for dispatch to customers.
Conclusion
Polyurethane foam moulding plays a crucial role in the manufacturing of high-quality, durable products across a variety of industries. The versatility, durability, and customizability of polyurethane foam make it an ideal material for use in automotive, furniture, marine, and industrial applications. Whether it’s for acoustic foam, safety products, or comfort solutions, foam moulding continues to be an essential technology driving innovation and efficiency.
By utilizing advanced foam conversion techniques and ensuring rigorous quality control, companies like Acoustafoam are able to produce products that meet the specific needs of their clients, delivering exceptional performance and value. As industries continue to evolve, the demand for high-quality polyurethane foam moulding will only grow, cementing its place as a vital material in modern manufacturing.
Read also: Home Staging Services to Make Your Property Stand Out
Benefits of Polyurethane Foam Moulding
- Durability: Offers resistance to wear, tear, and abrasion, ensuring long-lasting products.
- Versatility: Can be molded into various shapes, sizes, and textures for different applications.
- Acoustic Properties: Excellent for soundproofing and noise reduction in various industries.
- Customization: Tailored solutions for specific requirements, from automotive to furniture.
- Energy Efficiency: Acts as an effective thermal insulator, reducing energy costs.
The widespread use of foam moulding, particularly polyurethane foam, highlights its importance in creating products that are both functional and durable. Whether for enhancing comfort, improving safety, or reducing noise, foam moulding continues to meet the diverse needs of modern industries.